How technical innovation can enhance the lives of amputees
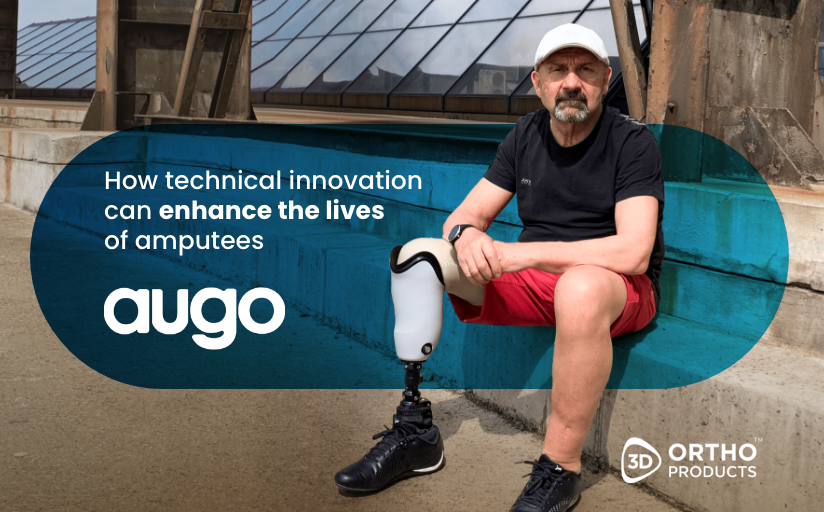
All clinicians want the very best outcome for their patients, and as a Prosthetist you know the strengths and limitations of the materials and components available to you. When it comes to helping amputees who are investing in a Trans Tibial (TT) prosthetic socket, you want them to be secure, comfortable and to regain the autonomy and independence they once had.
Innovative approaches, such as 3D scanning and printing, are becoming more usable and will definitely impact the way that clinics create and provide the socket interface to their patients and clients. In fact, the global 3D printing of medical devices market in terms of revenue was estimated to be worth $2.7 billion in 2022 and is poised to reach $6.9 billion by 2028; estimated to grow by 17% during the forecast period. Medical products include spectacle frames, operative guides and dental products and the prosthetic and orthotic fields are rapidly following as technology and materials allow configuration and strong, stable product manufacturing.
A fully integrated digital product design and manufacture direct from a patient scan is not quite with us yet, but the building blocks are coming. Patient scan and digital soft tissue modification and in clinic printed temporary check socket will be coming soon.
A final definitive TT socket is already available though. Made from a check socket or cast scan, the ISO-compliant Augo TT socket is designed to be strong, lightweight, and comfortable for your patients. Extending the boundaries of manufacturing and materials possibilities, the Augo socket is designed to give patients a prosthesis that’s lightweight, comfortable, strong, and 100% personal to them.
At 3D Ortho, we supply the Augo TT prosthetic socket. Designed by experts with over 30 years’ combined experience, Augo is a product of award-winning designers, computing and product engineers, Prosthetists and surgeons bringing together design, 3D scanning and printing, as well as market-leading materials and techniques.
To create life-changing results, Augo is:
100% custom
With 99.7% printing accuracy, the fit of Augo ensures the patient is comfortable and secure allowing a return to active life, improving their health. The design process ensures that the Augo is 100% custom to every patient., improving patient confidence wearing a TT socket that is completely bespoke to their needs.
Controllable
The design freedoms that 3D printing allows brings the ability to combine materials with precision for increased clinical and user control, plus comfort within the prosthesis. These aspects bring better outcomes and a more natural gait pattern, improving independence and confidence.
Lightweight strength
The compromises between reliable strength and weight are difficult to predict using traditional manufacturing methods, resulting in overweight or under-designed prosthetic socket manufacture. Using advanced design and materials knowledge, the Augo TT socket has been created to be a strong but lightweight interface that meets the requirements of the international standard, ISO 10328. Lighter weight and good fit means reduced energy expenditure and reduced fatigue as the patient returns to daily life.
Overall, we understand that in order to enhance an amputee’s care, you need to offer a TT prosthetic socket that is well-fitted, comfortable, and allows them to be in complete control. And with the technological advances of 3D scanning and printing, we are able to offer clinicians the opportunity to create a product that helps patients regain the independence they once had.
To discover more about the award-winning technology we can offer your clinic, go to our technology page. And for more information on Augo and the different prostheses we offer, visit our Augo page.